Frequently Asked Questions
Sizing & Selection
To properly size a breather valve, follow these steps:
Step 1. Determine Tank Specifications
- Measure the tank diameter and height.
- Identify the tank’s location and the environmental conditions it will be exposed to.
- Collect the Material Safety Data Sheet (MSDS) for the media stored in the tank, which includes:
*Media flash point
*Media boiling point
*Latent heat of vaporization
*Relative molecular mass of vapor.
Step 2. Calculate Maximum Flow Rates
Establish the maximum filling rate of the tank (in cubic meters per hour).
Establish the maximum emptying rate of the tank (in cubic meters per hour).
Step 3. Set Pressure and Vacuum Requirements
*Determine the set internal pressure (in mbar) that the valve must release.
*Determine the set vacuum pressure (in mbar) that the valve must handle.
*Consider the set temperature and specify whether the vent type will be pipe-away or atmospheric.
Step 4. Select Valve Size
*Based on the required flow rates and set pressures, use appropriate calculations to determine the valve size. Utilize standards such as API 2000 or ISO 28300 for precise sizing guidelines. Many manufacturers provide sizing software or charts to aid in selecting the correct valve size.
*The valve size can range from 2″ to 12″ (50 to 300 mm), depending on the application requirements and flow calculations.
Step 5. Material and Additional Features
*Choose the valve material based on the media’s compatibility and environmental conditions. Options include aluminum, ductile iron, stainless steel, carbon steel, and various alloys.
*Consider additional features like protective coatings, alarm sensors, or special designs (e.g., flame arresters, spring-loaded or weight-loaded mechanisms) as needed for specific applications.
Step 6. Utilize Manufacturer Support
If the size is not clear, many manufacturers offer a valve sizing service to provide optimum valve performance and cost-effective technical specifications. We offer sizing and calculation services tailored to specific customer requirements.
By following these steps, you can ensure that the breather valve is correctly sized for your application, providing effective protection against over-pressure and vacuum conditions in your storage tanks.
Produtos
Uma válvula de respiração (válvula de alívio de pressão/vácuo) foi projetada para proteger tanques de armazenamento, sistemas de processo e equipamentos de pressão excessiva e condições de vácuo. Essas válvulas permitem a ventilação controlada de gases ou vapores e ajudam a manter um ambiente de trabalho seguro, impedindo os danos ao tanque e minimizando a perda de produto devido à evaporação.
As válvulas de respiro funcionam usando paletes carregados de peso ou com mola para controlar o fluxo através da válvula. Quando a pressão interna ou o vácuo atinge um ponto de ajuste, o palete levanta o assento para permitir o fluxo. Isso evita as perdas de emissão até muito perto da pressão definida e impede a ingestão de ar até muito perto do vácuo definido.
- Alta capacidade de fluxo de um tamanho de válvula compacta.
- Ampla gama de configurações de pressão e vácuo para máxima proteção do tanque.
- Minimização da perda e evaporação de gás, resultando em economia econômica.
- Conformidade com regulamentos rigorosos de controle de emissões.
- O design modular permite a personalização para requisitos específicos.
As válvulas de respiro podem ser construídas a partir de vários materiais, incluindo alumínio, aço inoxidável, aço carbono, ferro dúctil e ligas como C276. A escolha do material depende do aplicativo específico e do tipo de mídia que está sendo tratado.
As aplicações comuns incluem a proteção de tanques de armazenamento em indústrias como farmacêutica, alimentos e bebidas, processamento químico e indústrias petroquímicas. Eles também são usados em sistemas onde os vapores precisam ser canalizados ou ventilados para a atmosfera.
As válvulas de respiro são projetadas e testadas de acordo com padrões como API 2000: 2014 e EN ISO 28300: 2016. Eles também se reúnem na Diretiva Europeia 2014/34/UE para equipamentos usados em atmosferas potencialmente explosivas (ATEX).
Selecting the right breather valve involves considering factors such as tank size, media characteristics (flash point, boiling point, latent heat of vaporization, molecular mass), location, maximum filling and emptying rates, and the required set pressure and vacuum settings. Consulting with a Yee Valve expert and using a valve sizing service can help ensure optimal performance and cost-effectiveness.
A inspeção e manutenção regulares são necessárias para garantir que as válvulas de respiro operem corretamente. Isso inclui a verificação de qualquer bloqueio, garantindo que os paletes e os assentos estejam limpos e livres de detritos e verificar se as pressões e aspiradores definidos são precisos. Os procedimentos de manutenção devem seguir as recomendações do fabricante para manter a segurança e a eficiência.
Um registro de chama é um dispositivo de segurança instalado em equipamentos que contém gases ou vapores inflamáveis. Impede a propagação de chamas e explosões, apagando a frente da chama antes que ela possa atingir o lado protegido do dispositivo.
Os prisioneiros de chama funcionam resfriando a frente da chama através de uma série de passagens estreitas ou "lacunas de extinção". Essas lacunas são projetadas para serem pequenas o suficiente para extinguir a chama, permitindo que os gases passem.
- Deflagração dos prisioneiros de chama: Proteja contra explosões onde a chama se propaga em velocidades subsônicas.
- Prisioneiros de chamas de detonação: Projetado para condições mais graves, onde a frente da chama viaja em velocidades supersônicas, produzindo ondas de choque.
- PRANTES DE FLAME FIM DE LINHA: Instalado no final de um pipeline para proteger contra fontes externas de ignição.
- PRANTES DE FLAME em linha: Instalado dentro do pipeline para impedir a propagação de chamas dentro do sistema de tubulação.
Os prisioneiros de chama são comumente usados em sistemas para gerar, armazenar e transportar gases e líquidos inflamáveis, como plantas de processamento químico, refinarias de petróleo, instalações de armazenamento de gás e oleodutos.
A inspeção e manutenção regulares são essenciais para que os prisioneiros de chamas funcionem corretamente. As principais tarefas de manutenção incluem:
- Inspeção inicial três meses após o comissionamento.
- Inspeções anuais no mínimo para processos limpos.
- Inspeções adicionais se uma explosão for detectada ou se houver sinais de dano ou corrosão.
- Limpeza para remover detritos, insetos ou corrosão que podem bloquear os elementos de têmpera.
- Verifique se o registro de chama está instalado corretamente de acordo com as condições operacionais.
- Verifique se nenhuma modificação não autorizada foi feita.
- Verifique se há bloqueios, corrosão e danos mecânicos.
- Confirme que todos os prendedores estão seguros e apertados com o torque necessário.
- Registre todas as atividades de manutenção com precisão.
Os prisioneiros de chama mal mantidos podem deixar de fornecer proteção adequada contra explosões, levando potencialmente a danos catastróficos de equipamentos e riscos de segurança. Questões comuns incluem elementos bloqueados, corrosão grave e danos mecânicos, o que pode prejudicar a eficácia do registro da chama.
Os prisioneiros de chama devem ser usados nas condições específicas em que foram projetadas e testadas. Eles estão disponíveis em várias configurações para se adequar a diferentes sistemas de tubulação, e o modelo correto deve ser selecionado com base no tipo de gás, pressão de operação e faixa de temperatura.
- Garanta a compatibilidade com as condições do processo, incluindo o tipo de gás e a pressão.
- Siga as diretrizes de torque para conexões flangeadas.
- Posicione o Relrete de Chama corretamente para facilitar a manutenção futura.
- Verifique se há vazamentos após a instalação para garantir uma vedação adequada.
- Não use os olhos de levantamento para levantar todo o conjunto do pára -quedas da chama; Eles são apenas para lidar com o alojamento durante a inspeção e manutenção.
- Evite conexões de drenagem, instrumentação e limpeza da tubulação para uma linha comum para evitar o desvio da chama.
- Substitua os elementos de chama danificados imediatamente, pois eles podem tornar ineficazes o registro da chama.
Termo de pagamento
Na Yee Valve, somos uma empresa familiar que integra habilmente a fabricação e o comércio de válvulas industriais. Nossa sede estratégica fica em Taipei, Taiwan, apoiada por três fábricas de última geração na China continental.
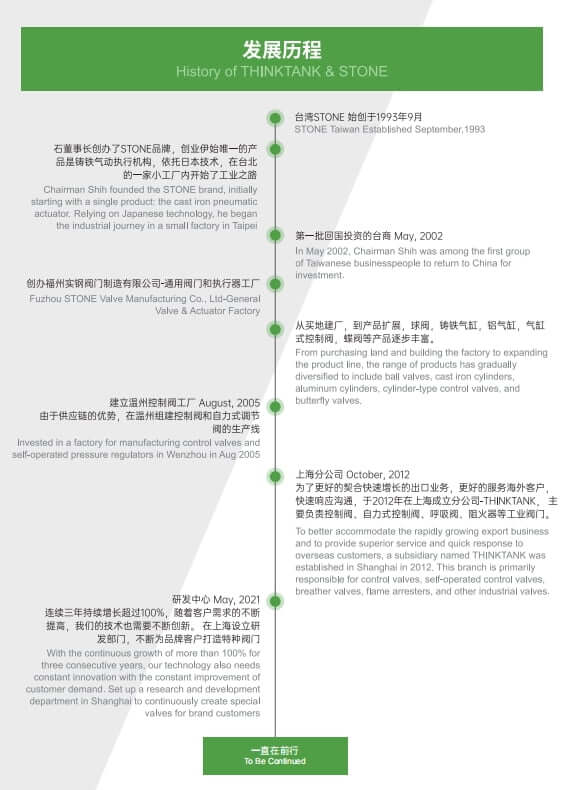
- Pague 30% adiantado e 70% antes do envio por TT (Produtos Padrão)
- Pague 100% antecipadamente por T.T. (Produtos Especiais)
- 100% L/C à vista de clientes especiais e L/C devem ser emitidos do banco de primeira classe do mundo. (Mercados especiais)
After-Sales Service & Technical Support
1. Technical Assistance
Yee Valve offers expert guidance for valve selection, installation, and maintenance. Customers can contact technical support via phone, email, or fax for any queries or issues related to our products. Also, we provide unique solutions to meet specific customer requirements, including custom designs and material options to suit various industrial applications .
2. Documentation and Certification
Compliance and Standards
All valves are designed and manufactured in compliance with relevant international standards such as API 2000 and ISO 28300. Yee Valve provides necessary documentation, including compliance certificates, user manuals, and test certificates to assure product quality and safety.
Product Manuals
Detailed product manuals and technical datasheets are provided to help customers understand the specifications and operational procedures of our valves.
3. After-Sales Support
Warranty Services
Yee Valve offers warranty services for our products, ensuring that any manufacturing defects or operational issues are addressed promptly. The warranty terms are provided at the time 12-18 months of purchase, and customers can request repairs or replacements as needed.
Spare Parts Availability
We maintain a stock of essential spare parts to facilitate quick replacements and minimize downtime. Customers can order spare parts directly from Yee Valve to ensure compatibility and reliability.
4. Maintenance and Repair Services
Preventive Maintenance
Yee Valve provides guidelines for preventive maintenance to help extend the lifespan of their valves and ensure continuous, reliable operation. Regular maintenance schedules and procedures are outlined in the product manuals.
Repair Services
In case of valve malfunction or damage, Yee Valve offers repair services performed by trained technicians. Customers can send their valves to authorized service centers or request on-site repair services depending on the severity of the issue.
5. Training and Support Programs
Training Programs
Yee Valve conducts training programs for customers to educate them on proper valve handling, maintenance, and troubleshooting techniques. These programs can be conducted on-site or at Yee Valve’s training facilities.
Technical Workshops
Periodic technical workshops and seminars are organized to keep customers updated on the latest advancements in valve technology and best practices in valve management.
6. Customer Feedback and Improvement
Feedback Mechanism
Yee Valve values customer feedback and has established mechanisms to collect and act on customer suggestions and complaints. This feedback helps in improving product quality and service standards.
Pedidos de problemas
When you make an order to Yee Valve, here are the steps you should follow based on the documents provided:
1. Verify the Order Details
Ensure that all order details, such as the model, quantity, and specifications match your request. Check the specific models ordered and their corresponding specifications against the provided documents.
2. Check the Material Specifications
Confirm that the materials listed for each valve component match what you ordered. For instance, body materials (e.g., Aluminum, AISI 316) and gasket materials (e.g., expanded graphite, PTFE) should align with the order specifications.
3. Dimensions and Connection Types
Validate that the dimensions (size, weight, etc.) and connection types (flanged, threaded, etc.) are correct. Make sure the dimensions of each valve (e.g., DN 50, DN 100) are as per the order.
4. Pressure and Vacuum Settings
Verify that the pressure and vacuum settings are correctly calibrated according to the order. Check if the valves are set to the correct pressure/vacuum relief settings required by you.
5. Accessory and Add-on Features
Ensure that any additional features or accessories (like proximity switches, flame arresters, or temperature sensors) requested by you are included and properly installed.
6. Documentation and Certification
Check that all necessary documentation, including test certificates, compliance certificates (e.g., ISO 9001, API Std 2000), and user manuals, are included with the shipment. Verify certifications for pressure equipment directives if applicable.
7. Quality Control and Final Inspection
Conduct a final inspection to ensure all valves are free from defects and meet quality standards. Confirm that the valves have passed all required tests and quality checks before shipping.
Shipping & Warranty
Todas as válvulas da Válvula Yee são cobertas com uma garantia de 12 meses a partir da data de instalação ou de 18 meses de garantia a partir da data da remessa, o que ocorrer mais cedo. O escopo da garantia é coberto apenas para defeitos de fabricação. Se uma falha da válvula for devida à operação incorreta pelo cliente, a garantia não será aplicável.
Todos os produtos enviados são documentados e fornecemos serviços OEM para muitas marcas sem qualquer informação sobre o fabricante dos produtos. Quaisquer desenhos, instruções de operação, relatórios de testes, etc., pertencem ao proprietário da marca.